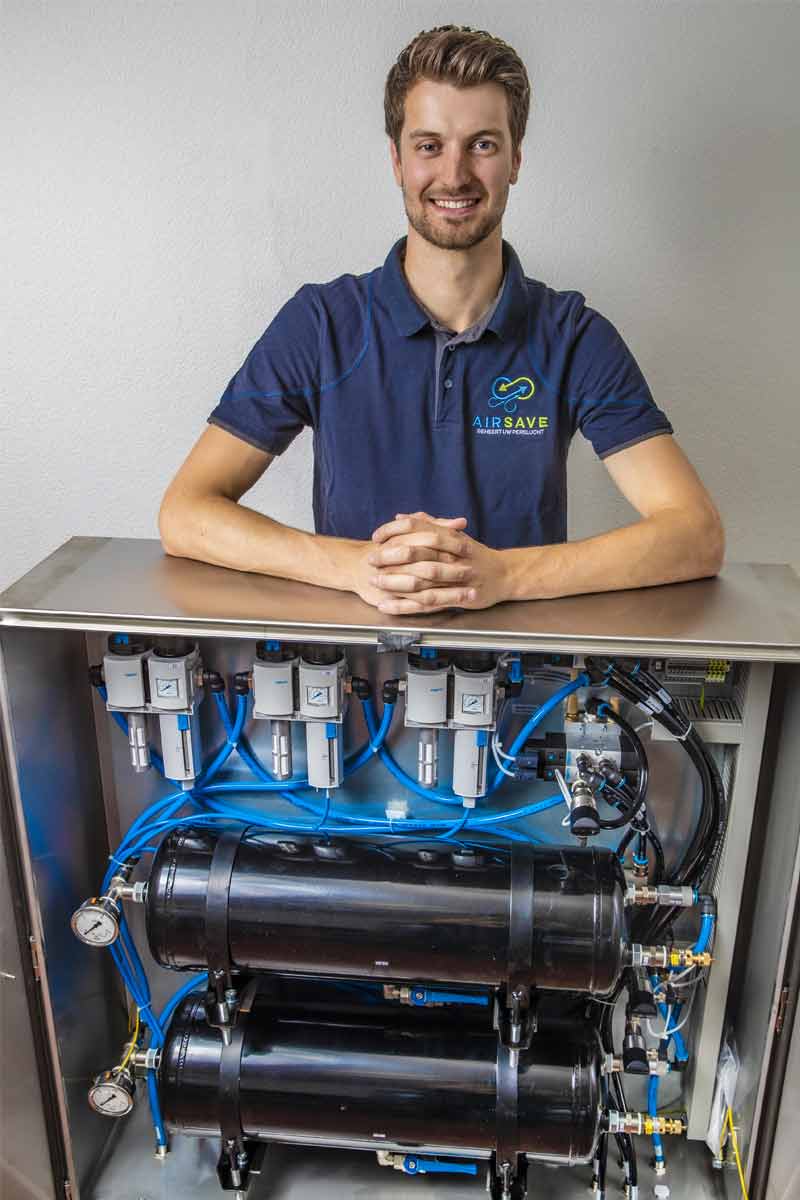
Airsave
During his traineeship at banknote paper supplier VHP Security Paper, Pim Duterloo developed a method for the early detection and reparation of compressed air leaks in the plant’s production line. This method helps reduce energy waste, leads to fewer breakdowns, and provides significant savings of up to tens of thousands of euros. The method proved so successful that Pim decided to specialise in this process. In 2017, he founded his own business, Airsave.
Airsave is a full-service partner, not just for leak detection
Airsave’s activities often start with a leak assessment, but their services go beyond that. Airsave specialises in the maintenance and optimisation of entire industrial compressed air installations. This includes every component that comes after the compression chamber. They help businesses cut back on both their downtime and their energy costs. They also provide independent consultancy services on compression chambers. This can vary from complete ISO audits of the compressed air network (from the compressor to the final user) to quotation assessments from compressor suppliers for upgrading and renewing compressor parks.
ROI in less than a year
Any leaks are reported together with a calculation of how much compressed air is lost annually. After compiling a detection report, an estimate is given of what the required repairs and parts will cost. When comparing the repair costs with the annual savings, the costs can often be recovered within a year. On average, some 60 networks are reviewed every year. For each network, the annual energy savings can sometimes amount to tens of thousands of euros and tonnes of reduced CO2 emissions.
Partnerships
Airsave also works when needed with specialised partners, each with their own specific expertise, to maintain and optimise entire compressed air installations. Airsave carries out a lot of work independently, such as placing or replacing new components or maintaining existing facilities. These include valves, valve islands, pneumatic control boxes, electro-pneumatic drive systems, air treatment and coupling materials. For these day-to-day operations, parts are kept in stock and on hand for fast delivery from their own warehouse.
Airsave also works together with or alongside the technical services of their clients’ manufacturing divisions. Measurements can take place during the production process, and the maintenance and replacement of parts are often incorporated into scheduled maintenance breaks.
The future
Detecting and repairing compressed air leaks is a niche market, and Airsave is a specialist in the field. That is why many installation companies and compressor suppliers often choose to work with Airsave.
Export countries: Belgium and Germany
Airsave
During his traineeship at banknote paper supplier VHP Security Paper, Pim Duterloo developed a method for the early detection and reparation of compressed air leaks in the plant’s production line. This method helps reduce energy waste, leads to fewer breakdowns, and provides significant savings of up to tens of thousands of euros. The method proved so successful that Pim decided to specialise in this process. In 2017, he founded his own business, Airsave.
Airsave is a full-service partner, not just for leak detection
Airsave’s activities often start with a leak assessment, but their services go beyond that. Airsave specialises in the maintenance and optimisation of entire industrial compressed air installations. This includes every component that comes after the compression chamber. They help businesses cut back on both their downtime and their energy costs. They also provide independent consultancy services on compression chambers. This can vary from complete ISO audits of the compressed air network (from the compressor to the final user) to quotation assessments from compressor suppliers for upgrading and renewing compressor parks.
ROI in less than a year
Any leaks are reported together with a calculation of how much compressed air is lost annually. After compiling a detection report, an estimate is given of what the required repairs and parts will cost. When comparing the repair costs with the annual savings, the costs can often be recovered within a year. On average, some 60 networks are reviewed every year. For each network, the annual energy savings can sometimes amount to tens of thousands of euros and tonnes of reduced CO2 emissions.
Partnerships
Airsave also works when needed with specialised partners, each with their own specific expertise, to maintain and optimise entire compressed air installations. Airsave carries out a lot of work independently, such as placing or replacing new components or maintaining existing facilities. These include valves, valve islands, pneumatic control boxes, electro-pneumatic drive systems, air treatment and coupling materials. For these day-to-day operations, parts are kept in stock and on hand for fast delivery from their own warehouse.
Airsave also works together with or alongside the technical services of their clients’ manufacturing divisions. Measurements can take place during the production process, and the maintenance and replacement of parts are often incorporated into scheduled maintenance breaks.
The future
Detecting and repairing compressed air leaks is a niche market, and Airsave is a specialist in the field. That is why many installation companies and compressor suppliers often choose to work with Airsave.
Export countries: Belgium and Germany