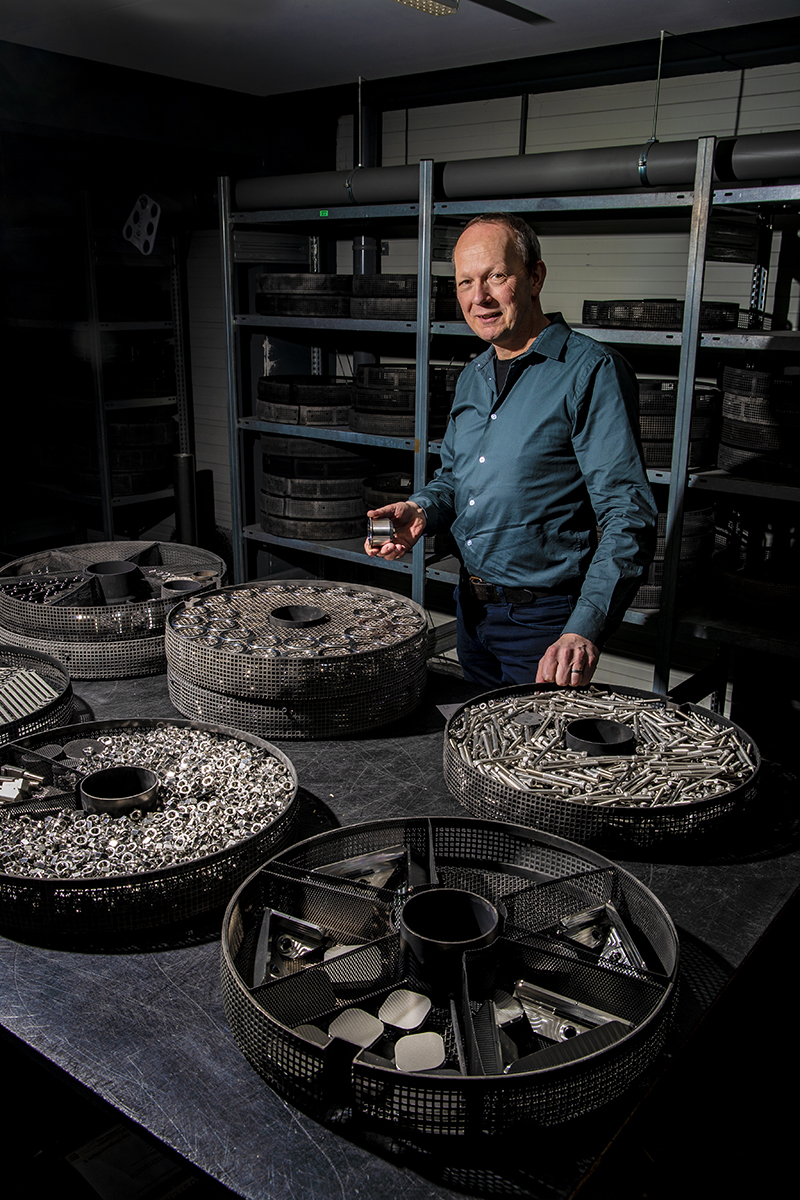
Bodycote
Kolsterising is the core business of Bodycote Hardingscentrum BV in Apeldoorn. Kolsterising is a new name for what is traditionally known as the ‘hardcor process’. The term ‘hardcor’ is a combination of the terms ‘hardening’ and ‘corrosion resistance’. The actual process name, Kolsterising, is named after the head of the research group that invented the process in the 1980s, Ben H. Kolster (1938-2011). The process was developed in the early 1980s and has led to an increased range of applications for austenitic and duplex stainless steel materials. Around 1998, the Apeldoorn-founded company was taken over by the British concern Bodycote, and the process name was changed into Kolsterising.
Applications
Kolsterising is a surface hardening technology that increases the surface hardness through carbon diffusion without significantly altering the size, shape, or colour of the material. This method can be applied to austenitic and duplex stainless steel materials and nickel. Typical examples of this material group include AISI304, AISI316 and Duplex 2205. The process hardens the surface of these materials (up to about 1000 to 1200 HV) without loss of corrosion resistance, particularly compared to other methods such as nitriding processes. It is a revolutionary technique that increases the lifespan of parts such as pumps by applying a durable, wear-resistant layer.
Full in-house service
The machines that are required for this highly confidential process are developed in-house. Today, these machines are not only found in Apeldoorn, where they are manufactured. They have found their way to various parts of the world at Bodycote customer sites. Moreover, the Apeldoorn site also supplies many countries directly. The customers send in their stainless steel parts and products, which are then quickly and reliably processed and hardened, cleaned, and returned corrosion-free as ever to the customer — all in all, an essential and valuable process.
Countries: Germany, Belgium, Spain, Poland, Italy, Switzerland, Ireland, Israel, Japan, China, India
Bodycote
Kolsterising is the core business of Bodycote Hardingscentrum BV in Apeldoorn. Kolsterising is a new name for what is traditionally known as the ‘hardcor process’. The term ‘hardcor’ is a combination of the terms ‘hardening’ and ‘corrosion resistance’. The actual process name, Kolsterising, is named after the head of the research group that invented the process in the 1980s, Ben H. Kolster (1938-2011). The process was developed in the early 1980s and has led to an increased range of applications for austenitic and duplex stainless steel materials. Around 1998, the Apeldoorn-founded company was taken over by the British concern Bodycote, and the process name was changed into Kolsterising.
Applications
Kolsterising is a surface hardening technology that increases the surface hardness through carbon diffusion without significantly altering the size, shape, or colour of the material. This method can be applied to austenitic and duplex stainless steel materials and nickel. Typical examples of this material group include AISI304, AISI316 and Duplex 2205. The process hardens the surface of these materials (up to about 1000 to 1200 HV) without loss of corrosion resistance, particularly compared to other methods such as nitriding processes. It is a revolutionary technique that increases the lifespan of parts such as pumps by applying a durable, wear-resistant layer.
Full in-house service
The machines that are required for this highly confidential process are developed in-house. Today, these machines are not only found in Apeldoorn, where they are manufactured. They have found their way to various parts of the world at Bodycote customer sites. Moreover, the Apeldoorn site also supplies many countries directly. The customers send in their stainless steel parts and products, which are then quickly and reliably processed and hardened, cleaned, and returned corrosion-free as ever to the customer — all in all, an essential and valuable process.
Countries: Germany, Belgium, Spain, Poland, Italy, Switzerland, Ireland, Israel, Japan, China, India